石英晶體中的結構型雜質主要分為兩類:一類晶格替代雜質,是指正三價B3+、Al3+、Fe3+、正四價Ti4+、Ge4+及正五價的P5+原子與硅氧四面體中正四價的Si4+原子類質同象替代,代替Si4+原子形成新的四面體;另一類是電荷補償雜質,這類結構型雜質是發生在四面體間隔通道位置;由于正三價、正五價原子替代正四價的Si原子形成新的四面體,造成了晶格內部電荷不平衡;作為電荷補償的一價Li+、Na+、K+、H+、OH-離子及二價Fe2+離子,在四面體間隔通道位置形成電荷補償,實現電荷平衡。
由于這些元素離子(Li+、K+、Na+、H+)半徑大(0.078~0.178nm),它們只能賦存于硅氧四面體骨架空隙之中;因此易于從石英晶體中擴散出來,同時也易從外界擴散進入石英晶體中。
賦存于石英晶體結構中的微量元素因受到硅氧四面體的束縛而很難被活化,利用常規的選礦技術(磁選、浮選、酸浸)難以實現有效的分離;國內“高鐵堿鋁型”石英均含有大約1000×10-6的晶格Al,導致這些石英礦床的品質較低。國內外各科研單位又因技術保密等原因各自為戰,導致石英晶格雜質的系統性分離研究鮮著報端;對晶格雜質去除效率較高的一些高溫氧化/氯化焙燒技術又因成本高、技術含量高在國內鮮有工業化應用。
目前,高品質石英晶體結構中微量元素的先進分離技術主要有氯化焙燒純化技術、真空焙燒-酸浸純化技術等。氯化焙燒與真空焙燒-酸浸純化技術在用于分離石英中微量晶格雜質時須用到高溫氧化、氯化環境。分離工藝對生產裝備的壽命要求高,要求其在1000~1500℃氧化、氯化性條件下連續、穩定、安全的工作;裝備成本較高,藥劑成本非常低,但氧化、氯化反應受到石英砂高溫堆密度制約,分離速度較慢,主要適用于原礦品位較高的超高純石英加工,提純后石英砂品位可達到5N級及以上。其中氯化焙燒技術已有工業化實踐,真空焙燒-酸浸純化技術尚在實驗室完善階段。
1、氯化焙燒純化技術
在傳統的氯化焙燒純化技術中,石英砂通常在Cl2或HCl氣體氣氛中被加熱到1000~1200℃。主要微量金屬元素(例如在石英晶格中結合的Al3+、Fe3+和Ti4+)擴散到石英晶粒的表面/界面,然后與電離出的Cl-反應,形成低沸點氯化物得以被迅速去除。即使在1000~1200℃,硅氧四面體的結合能力依舊很大,金屬元素仍以極低的擴散速率向石英表面/界面擴散,嚴格地限制了氯化反應的反應速率。
在較高的溫度(1200~1500℃)下,固體石英砂明顯熔化形成固溶體,由于總孔隙率的降低,石英顆粒的體積密度大大增加;在這種溫度下,盡管金屬元素已經被活化,但固溶體石英失去了許多允許晶格雜質與Cl-反應的活性界面。在較高的溫度下,氯化率實際上更低。因此,高溫條件下石英中的晶格雜質在擴散速率與反應速率之間的矛盾是迫切需要解決的最關鍵問題之一。
由于傳統氯化焙燒純化技術溫度較高,一些鹽類氯化劑被引入到石英提純中以降低焙燒溫度并提升分離效率。采用包括NaCl和KCl在內的高效氯化劑對高品質石英進行提純,石英的晶體結構可以被陽離子嚴重破壞,從而促進從α-石英到β-石英或方晶石的快速相變??焖傧嘧儠越榭缀突钚越缑娴男问叫纬韶S富的晶體缺陷,為相分離提供可能的活性位點。氯化劑中的陽離子(K或Na)可以被氯氣或氯化氫氣體去除,從而實現對結構性和面網間堿金屬元素雜質的綜合去除。同時,應該注意的是,NaCl和KCl在石英加工中的用量必須嚴格限制。
2、真空焙燒-酸浸純化技術
真空焙燒-酸浸純化技術是將氯化焙燒純化技術的活化與分離步驟分化,在高溫真空焙燒過程實現晶格雜質的活化與富集,在酸浸過程實現表面、界面、缺陷處的固-液相反應,完成晶格雜質的酸解分離;可降低分離反應的內擴散與化學反應阻力,提升分離效率。
鐘樂樂等利用真空焙燒設備在高真空(0.01Pa)、高溫(約1500℃)條件下焙燒石英砂(3h),再利用混合酸體系(HCl-HF-HNO3)浸出石英中的雜質,石英中Al、Fe、K、Na、Ca、Mg含量低至7.9、0.65、1.80、15、3.3及0.34g/g,各雜質元素相對于原礦去除率分別為:89.7%、99.0%、94.2%、68.0%、91.5%及87.8%,制備得到SiO2含量為99.996%的超高純石英。
利用XRD慢掃描結合ICP-MS技術分析了晶胞參數、真空焙燒溫度與雜質石英中含量的影響。研究認為:Al主要存在于石英晶格的a-b平面內,Fe、K、Na主要分布于石英晶格中c軸方向,真空焙燒對石英晶格沿c軸分布的雜質去除更有利。
經高溫真空焙燒,石英顆粒表面及內部均形成大量的裂隙,這些裂隙主次有序,遍布石英顆粒內部。顆粒內部沿焙燒-水淬形成的裂紋擴展,形成較大裂隙,沿大裂隙生成方向,形成一系列較小的細裂紋,密集分布于整個石英顆粒內部。這些裂隙的形成原因:1)石英內部氣液包裹體受熱膨脹,包裹體內部壓力劇增,顆粒外部壓力很?。?.01Pa),氣液包裹體爆裂導致石英晶體斷裂形成裂隙;2)在焙燒后冷卻過程中,石英顆粒內外部溫度不均;向α石英轉變時,形成的微裂紋無法恢復,反而阻礙了晶型轉變形成過多的裂紋。
經高溫真空焙燒,晶格雜質能夠被活化、富集至石英晶體表面、界面、缺陷處,利用混合酸體系(HCl-HF-HNO3)在高溫(280℃)反應釜中浸出、純化高溫真空焙燒后的石英砂,可有效腐蝕石英顆粒表面和焙燒形成的缺陷,分離富集的微量晶格雜質。
3、相變熱活化與分離機制
石英在自然界存在著多種同質多相變體,在石英多種同質多相變體之間發生轉變的過程中,石英的晶體結構會發生變化,晶格內部雜質賦存狀態也會隨之發生改變。石英純化過程中,反應溫度在晶型轉變溫度點附近,會有利于石英中雜質金屬元素擺脫石英晶格的束縛,擴散遷移出石英晶體界面。
870℃/1470℃左右真空焙燒:β-石英轉變為β-鱗石英/β-鱗石英轉變為β-方石英,雜質金屬元素Al、Fe(晶格替代)的去除率隨焙燒溫度的升高(850~890℃/1450~1490℃)幾乎保持不變;雜質金屬元素Na、K的去除率隨焙燒溫度的升高先增加后趨于平緩(晶型轉變溫度),去除率不再大幅增加;870℃時的石英相變能夠釋放相當部分的四面體面網間填隙式的電荷補償雜質原子(Li、Na、K),而一些晶格替代雜質Al、Fe依然被束縛于四面體晶格上。充分應用石英的熱相變來提高晶格元素的擴散速率是可能解決擴散速率與反應速率矛盾的潛在方法。例如,在820℃時,β-石英被迅速加熱到920℃形成β-鱗石英;然后迅速冷卻到820℃;加熱程序在820~920℃間反復重復,以實現β-石英和β-鱗石英之間的迭代相變。雖然β-石英和β-鱗石英均屬于六方體系,但六方雙錐的β-石英被轉化為六方板狀的β-鱗石英,然后轉化為β-石英。在這個重復的相變過程中,在石英晶格中賦存的微量元素隨著一些特殊的Si-O鍵的迭代斷裂和恢復而不斷被激活,這種特殊的相變導致晶格雜質從石英內部向表面、界面連續的擴散。在石英相變過程中,Si-O鍵的規則斷裂可以顯著地降低了晶格雜質的活化能,快速相變導致密度的明顯變化,還會形成大量的晶體缺陷,為晶格雜質的表面富集和相分離提供更多的活化界面。
Cl2或HCl與高溫焙燒(反復相變)一起使用,可以有效地去除石英顆粒表面/界面/缺陷中富集的金屬元素。另一種方法是使用氫氟酸或磷酸溶液,而不是危險的Cl2或HCl氣體,以純化被高溫活化后的石英砂;因為許多晶格雜質在微小的晶體界面/缺陷周圍富集,高溫和壓力在浸出過程中是非常必要的。近年來,熱磷酸提純石英砂的加工技術以其低成本、高效率和“綠色”性能已經受到重視。
資料來源:《林敏,賈倩,劉子源,等.高純石英(SiO2)評述(二):晶格雜質的活化與分離技術[J].礦產綜合利用,2022(06):21-25》,由【粉體技術網】編輯整理,轉載請注明出處!
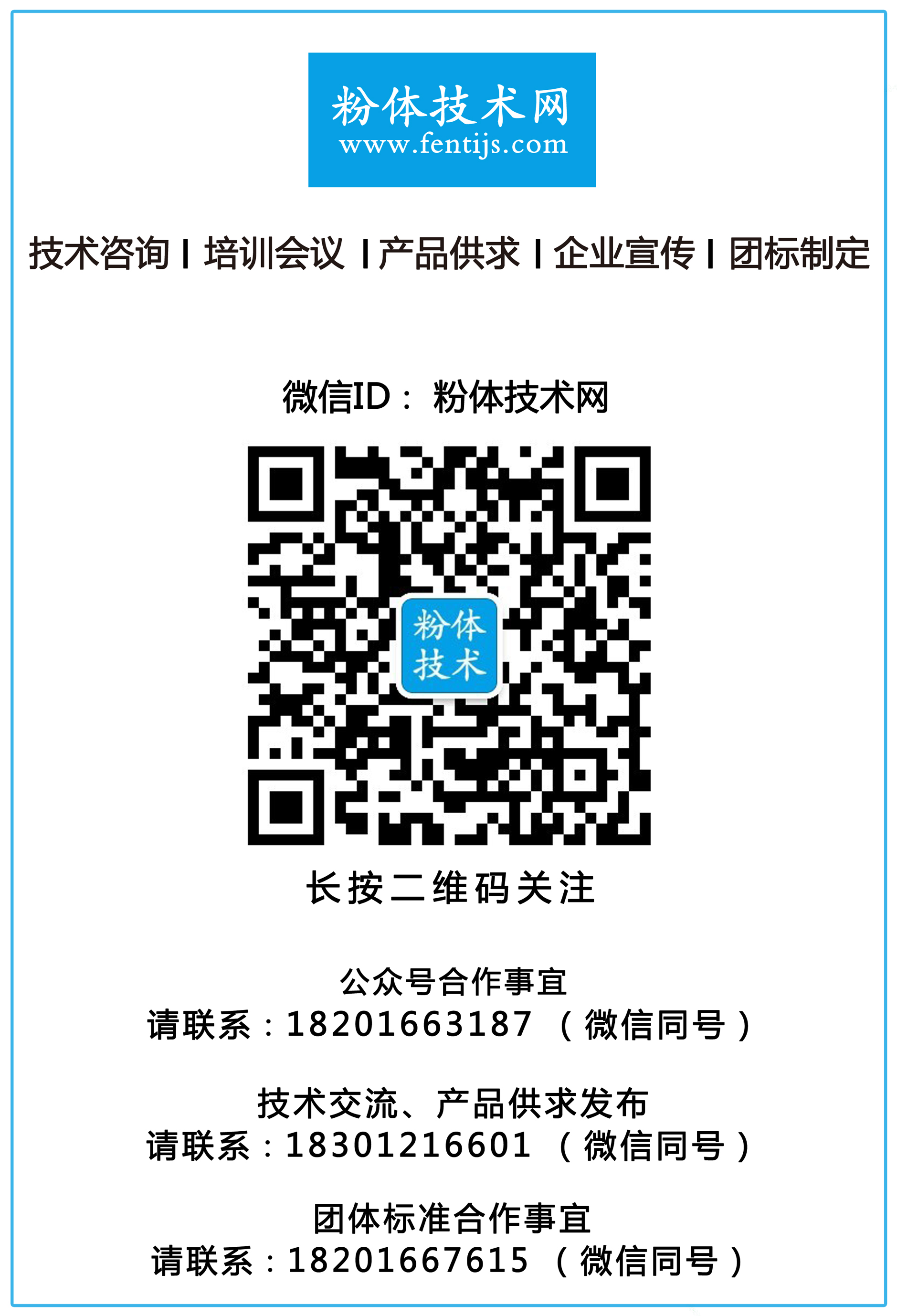
|