鋼鐵工業是CO2和固體廢物排放的最大工業來源之一。固體廢棄物主要包括煉鐵過程中產生的高爐渣和煉鋼過程中產生的鋼渣。根據鐵礦石的品位和所采用的工藝條件不同,2019年全球鋼渣和高爐渣產量分別約為2.4億噸和3.9億噸,其中中國約占53%和64%。由于鋼渣/高爐渣中含有30%~60%的CaO,越來越多的學者開始關注其高值化利用。
考慮到鋼渣/高爐渣為堿性廢棄物,各種類型的強酸如HCl、HNO3和H2SO4表現出90%左右的鈣浸取效率,包煒軍等使用TBP和乙酸的混合溶液選擇性地從鋼渣中浸取大約75%的鈣組分。
綜合考慮浸取效率和投資成本,采用各種循環銨鹽(NH4Cl、NH4NO3、CH3COONH4)選擇性地浸取鋼渣/高爐渣中鈣組分相對經濟,常溫常壓下,鈣浸取率可達65%左右。
此外,鋼渣的粒度對鈣的浸取率有明顯的影響,鋼渣粒度越小,比表面積越大,傳質速率越好,浸取效率越高。固液比是提高浸取效率的另一個重要參數。當固液比小于5g/L時,鈣的浸取效率最高(73%),當固液比大于100g/L時,鈣的浸取效率最低(6%)。此外,也有通過使用超聲等處理手段顯著將鈣浸取率從65%提高到96%。
碳酸化是指含鈣離子浸取液與CO2反應。為了在溫和條件下提高碳酸化效率,需要堿性物質(如氨水、氫氧化鈉)作為緩沖溶液調節pH。Park和Fan等采用NH4OH溶液首先將pH值提高到8.6祛除沉淀氧化鐵,向濾液中注入純CO2。進一步將pH提高到9.5,得到高純度的微細碳酸鈣產品。Wang等發現在100℃下,使用1.4mol/L硫酸氫銨(NH4HSO4)在3小時內從原料中浸取超過95%的活性鈣成分,并且通過調節pH值,在碳酸化階段制備高純度碳酸鈣。
四川大學岳海榮等提出了多級沉淀的熱還原技術,其中高爐渣先用硫酸銨((NH4)2SO4)在300~450℃下焙燒,使鈣成分轉化為硫酸鹽,相對溫和條件下用碳酸氫銨/碳酸銨(NH4HCO3/(NH4)2CO3)溶液進行均相碳酸化制備碳酸鈣產品。
Chiang等將高爐渣轉化為兩種有價值的產品:微細碳酸鈣和沸石材料。首先通過用有機酸選擇性地浸取鈣組分,然后對浸取液進行碳酸化來制備微細碳酸鈣。與此同時,浸取的固體殘渣在堿性溶液中水熱轉化,誘導了溶解/沉淀機制,導致形成微孔和中孔沸石材料。
鋼渣/高爐渣等由于其形成過程經歷了表面反應或高溫燒結,活性CaO組分通常位于晶體結構中,或被表面硅酸鹽或硫酸鹽包裹,導致其反應活性差、安定性較差。因此,有效剝離鋼渣/高爐渣等惰性組分與活性組分,消除其不穩定性,平衡礦化活性組分剝離速率與碳酸化反應速率是其碳酸化生產高附加值碳酸鈣產品的關鍵。
資料來源:《李文秀,楊宇航,黃艷,等.二氧化碳礦化高鈣基固廢制備微細碳酸鈣研究進展[J].化工進展:2022》,由【粉體技術網】編輯整理,轉載請注明出處!
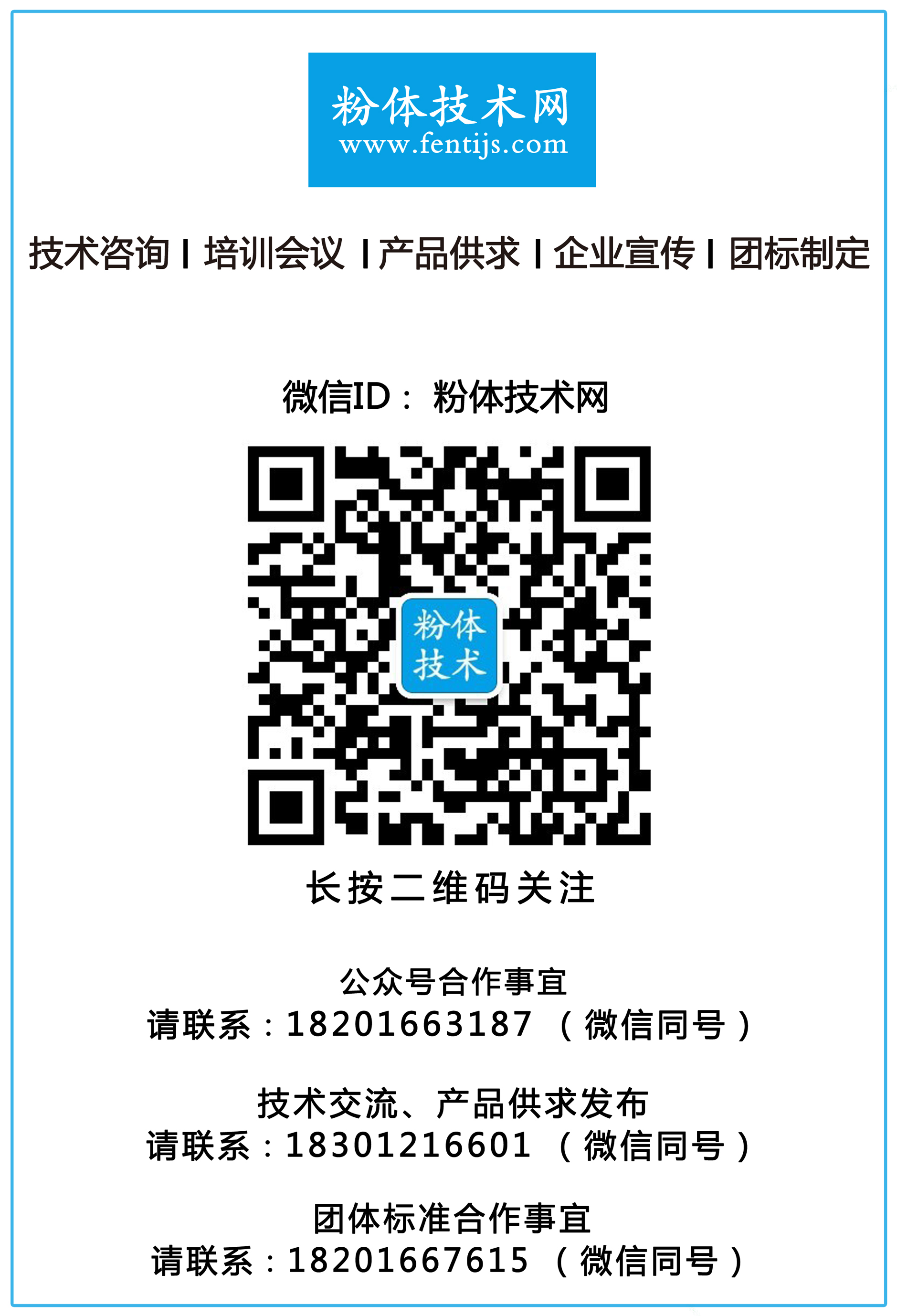
|