等靜壓石墨是上世紀40年代發展起來的一種新型石墨材料,具有一系列優異的性能。等靜壓石墨的耐熱性好,在惰性氣氛下,隨著溫度的升高,其機械強度反而升高,在2500℃左右時達到最高值;與普通石墨相比,結構精細致密,而且均勻性好;熱膨脹系數很低,具有優異的抗熱震性能;各向同性、耐化學腐蝕性強、導熱性能和導電性能良好;具有優異的機械加工性能。正是由于具有這一系列的優異性能,等靜壓石墨在化工、半導體、電氣、冶金、機械、核能及宇航等領域得到廣泛應用,而且,隨著科學技術的發展,應用領域還在不斷擴大。
1.等靜壓石墨的主要用途
1.1太陽能電池及半導體晶片用石墨
在太陽能、半導體行業中,大量使用等靜壓石墨,制作單晶直拉爐熱場石墨部件,多晶硅熔鑄爐用加熱器,化合物半導體制造用加熱器、坩堝等部件。近年來,太陽能光伏發電發展迅猛,光伏產業中的單晶硅和多晶硅生產對石墨需求量巨大。目前,單晶、多晶硅產品均朝大型化、高端化發展,對等靜壓石墨也有了更高的要求,即:更大規格、更高強度、更高純度。
1.2核石墨
等靜壓石墨具有中等的力學性能,特別出色的高溫力學性能,導熱系數大,線膨脹系數低。在高溫氣冷堆中,主要用作反射劑、慢化劑及活性區結構材料,同核燃料一道構成核燃料組件。在400~1200℃的溫度下,受高能γ射線和快中子的放射線,時間長達數年之久,容易造成輻照損傷,從而改變石墨的結構和性質,所以要求材料的石墨化度高、各向同性度好、組成均一、彈性模量低。目前,我國只能生產少量的高溫氣冷反應堆用核石墨,主要還是依賴進口。
1.3電極石墨
石墨無熔點,是電的良導體,抗熱震性好,是極佳的電火花加工電極材料普通石墨材料,為粗顆粒結構低密度各向異性石墨,不能滿足電火花加工的需求,而等靜壓石墨電極結構均勻、致密、加工精度高,可以滿足這方面的要求。
1.4 連續鑄造結晶器石墨及模具石墨
主要用于連續鑄造結晶器與超硬材料生產用能耐高溫、高壓的模具材料。 等靜壓石墨由于它的微粒子結構、較高的機械強度、均勻的熱傳導,使連鑄與模壓的產品表面光滑,內在質量高,使用壽命長,是結晶器的最佳材料。而且對于大型燒結材料,模具壁的厚度應盡可能薄,必須使用強度很高的細結構各向同性石墨。
1.5其它用途
在炭刷、機械密封、觸輪的集電板等處使用,要求加工精度的同時,高潤滑性和高導電性是極其重要的。普通石墨材料,需要用樹脂、金屬進行浸漬處理,以提高強度和氣密性,但在耐腐蝕和耐高溫性能上限制其使用范圍。
等靜壓石墨摩擦系數低、導熱性能好,常用作軸承、機械密封用密封環、活塞環等滑動摩擦材料。此外,等靜壓石墨還用于制作金剛石工具,光纖拉絲機的熱場部件(加熱器、保溫筒等),真空熱處理爐的熱場部件(加熱器、承載框等),以及精密石墨熱交換器。
2 等靜壓石墨的發展狀況
由于高密度各向同性碳材料的性能優良、用途廣泛、附加值高,各發達國家都投入較多的人力物力開發該材料。據日本相關資料,由于等靜壓石墨材料的開發,炭石墨材料的年產值每五年就翻一番。目前,我國高端等靜壓石墨產品主要依賴進口,有統計表明,其中約80%來自于日本,其余來自于歐美。
美國是世界上最早研制和生產等靜壓石墨的國家,上世紀50年代末就有產品面市。目前,在美國生產經營等靜壓石墨的著名企業有:POCO公司、尤卡碳素公司、大湖碳素公司、圣瑪麗工廠等。其中圣瑪麗工廠在上世紀90年代末,就能生產規格為Ф1250mm×2000mm的大型等靜壓石墨材料。
日本原子能研究所于1971年設立石墨材料研究室,設計研究多用途高溫氣冷堆用等靜壓石墨材料,很快便取得了突破性進展。
1978年,吳羽化學工業公司同東北協和炭素公司,聯合開發出了不使用粘結劑的,自燒結等靜壓石墨的工業生產技術。1999年,東洋碳素公司已批量生產Ф1500mm×2000mm的大規格等靜壓石墨,并具備生產Ф>2000mm的等靜壓石墨的能力。目前,日本的等靜壓石墨無論是在產量、質量、品種還是規格上都達到了世界先進水平,是我國高端等靜壓石墨產品的主要進口國。
我國在等靜壓石墨的開發方面,處于起步階段,與發達國家相比存在較大差距。中國科學院山西煤炭化學研究所、北京化工大學、湖南大學、天津大學、東新電炭公司等單位和企業,正在從事自燒結高性能碳材料相關方面的探索和研究。而連鑄結晶器石墨的研究與生產,開始于上世紀七十年代初;目前,國內從事該項目研究和生產的企業有蘭州炭素廠、上海炭素廠、東新炭素廠、哈爾濱炭素廠、哈爾濱電炭研究所、吉林炭素廠等,但制造工藝和產品性能與國外相比有較大差距。
3.等靜壓石墨的生產工藝
如圖1所示,為等靜壓石墨的傳統生產工藝流程。
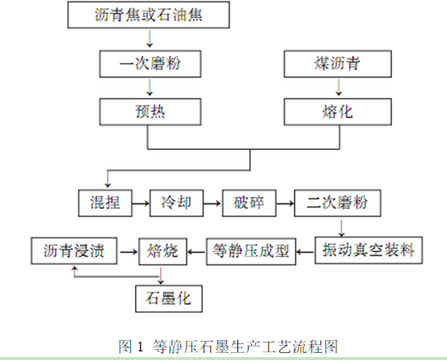
制備等靜壓石墨,一般需要使用結構上各向同性的碳質原料,并將其磨制成特定粒度的粉料。為避免粉料在壓制過程中出現定向排列的現象,需要應用冷等靜壓成型技術。為保證焙燒過程中,坯體內外溫度平衡,升溫必須十分緩慢。為了達到預期密度,一般需要進行多次的浸漬—焙燒循環。最后,樣品的石墨化周期也要比普通石墨材料長得多。
除上述傳統制備方法外,另外一種方法為自燒結法。自燒結法是以具有自燒結性的粉末為原料,不使用粘結劑,制造等靜壓石墨的方法。日本吳宇化學工業公司的生產方法是,對瀝青分兩階段進行特殊處理,得到特殊結構的原料,然后在不用粘結劑的情況下,直接壓制、焙燒和石墨化,制得高性能等靜壓石墨。由于相關的公開文獻很少,本文不介紹這種方法。
3.1 原料
生產等靜壓石墨的原料,主要包括骨料、粘結劑及少量添加劑。石油焦和瀝青焦是最常見的等靜壓石墨骨料,另外,天然石墨、無煙煤、炭黑等也常被用作骨料。
一般情況下,為了減小樣品在焙燒和石墨化過程中的收縮率,石油焦和瀝青焦需要在1200~1400℃下進行煅燒,去除水分及揮發分后才能使用。但是為了提高制品的機械性能和結構致密性,也有直接用生焦做原料生產等靜壓石墨的,例如日本東海炭素株式會社在其公開專利《各向同性石墨制造法》中,就是使用含氧量在4%以下的生焦炭作為骨料。生焦的特點是含有揮發分,具有自燒結性,與粘結劑焦同步膨脹和收縮。煤瀝青是最常用的粘結劑,酚醛樹脂等脂類物料也常被用作粘結劑。
例如清華大學在其公開專利《一種各向同性石墨制品及其制備方法》中,就將瀝青、酚醛樹脂、糠醛樹脂和環氧樹脂的脂類物料,均列為其粘結劑備用材料。
等靜壓石墨中的添加劑主要是硼及其化合物,用來促進碳材料的燒結,但也引入了硼元素雜質,可在純化過程中去處。
等靜壓石墨的性能受原料的影響極大,對原料的精選是能否生產出所需要的最終產品的關鍵環節。投料前必須對原料特性和均勻性進行嚴格檢測。
3.2 粉磨
粉磨,包括一次粉磨和二次粉磨。一次粉磨是指對原料中骨料的破碎,一般認為,骨料粒度越小,制得的最終產品的致密度、強度及各向同性度越好。等靜壓石墨的骨料粒度通常要求達到20μm以下,目前,最精細的等靜壓石墨,顆粒直徑為1μm,如美國的電火花用EDM-AF5型等靜壓石墨的粒徑,就達到了1μm。
要把骨料焦炭磨制成這么細的粉末,需要用到超微粉碎機。磨制平均粒度為10~20μm
的粉末需要使用立式輥磨機,而磨制平均粒度小于10μm的粉末就需要使用氣流磨粉機。二次粉磨,是指對混捏后的冷卻糊料的破碎,粒度可在幾十微米到幾百微米之間,利用立式輥磨機或球磨機就可完成。糊料經破碎、篩分,成為壓粉。
3.3 混捏
將磨制好的骨料粉末和粘結劑、添加劑等,按比例投入到加熱式混捏機中,進行充分混捏,使骨料顆粒表面均勻附著一層瀝青?;炷蠊に嚤容^簡單,需要控制好混捏的溫度和時間,混捏溫度根據所用粘結劑確定,一般不超過150℃;混捏時間根據骨料與粘結劑的比例確定,一般不低于1h?;炷笸瓿珊?,取出糊料,待其冷卻后進行二次粉磨。
3.4 等靜壓成型
等靜壓成型,是保證等靜壓石墨材料各向同性的關鍵工藝。等靜壓成型的基本原理是帕斯卡定律,即在充滿液體的封閉容器中,施加于流體中任一點的壓力,必以相同的數值傳遞到容器中的任一部位。在等靜壓成型過程中,壓力通過水等液體介質傳遞到橡膠模具上,各個方向上的壓力是相等的。這樣,粉料在模具中就不是按填充方向取向,而是按不規則排列方式被壓縮。
因此,盡管石墨在晶體學特性上是各向異性的,但是從整體上看,等靜壓石墨卻是各向同性的。 等靜壓石墨的成型大致分為三個步驟:裝料、升壓及降壓。將原料壓粉填充到橡膠模具中,通過高頻電磁振動,使得壓粉得到密實。裝完料后用手工對模具適當整形,然后將其密封。此時,模具內的粉料中還含有大量空氣,會影響制品的成型性能及致密度,所以還需要對密封后的模具進行抽真空,以排除粉料顆粒間的空氣。
生產某些球形產品時,則應先將粉料用模壓法預壓成球體,再置入相應尺寸的等靜壓成型的模具內,例如成都碳素有限責任公司在其公開專利《一種核石墨材料組合及預處理方法》中,就采用了先模壓成型,再等靜壓成型的工藝流程。
裝料完成后即將模具轉入高壓容器內進行壓制。加壓過程需要分階段逐步進行。例如,先將壓力升5MPa,保持一段時間,使模具內殘余氣體部分排出。此時,因粉料受壓而體積收縮,因此高壓容器內壓力略有下降。接著再次升壓至20MPa左右,排出部分氣體后粉料體積再次收縮,然后再升高壓力到所需的工作壓力,一般為100~200MPa,并在選定的高壓下保持一定時間(20~60min)后再降壓。降壓過程也需緩慢進行,因為粉料中必定還殘留有少量空氣,并隨著粉料的壓縮,體積急劇減小。如果壓力突然減小,這些壓縮的氣體就會迅速膨脹,從而導致坯體開裂。
目前,用于等靜壓石墨生產的冷等靜壓機最大規格為φ2150mm×4700mm,最高工作壓力180MPa。
3.5 焙燒
焙燒是除去坯體中揮發份,并使粘結劑焦化的過程,最高溫度一般不超過1250℃。在焙燒過程中,骨料和粘結劑之間發生復雜的化學反應,粘結劑在分解,釋放大量揮發分的同時,進行縮聚反應。在低溫預熱階段,生坯因受熱而膨脹,在隨后的升溫過程中,又因縮聚反應而體積收縮。生坯的體積越大,揮發分的釋放就越困難,同時,生坯表面和內部也越容易產生溫差、收縮不均勻等現象,這些都有可能導致坯體出現裂紋。等靜壓石墨由于結構細密,焙燒過程要求要特別緩慢,而且爐內溫度要非常均勻,尤其是在瀝青揮發分急劇排出的溫度階段,加熱過程要謹慎進行,升溫速度不能超過1℃/h,爐內溫差要求小于20℃,此工藝一般需要1個月以上的時間。
如天津錦美碳材料科技發展有限公司在其公開專利《一種各向同性石墨的制備方法》中所述,一次焙燒的最高溫度為1200℃左右,平均升溫速率為3℃/h。其中350~400℃,升溫速度:≤1℃/h;400~500℃,升溫速度:≤0.7℃/h;500~600℃,升溫速度:≤1℃/h。
3.6 浸漬
焙燒過程中,粘結劑揮發分被排出,并在制品中留下細微的氣孔,且幾乎都是開口氣孔。這些氣孔的存在,會損害制品的體積密度、機械強度、導電率、導熱率及抗化學反應性等。生產中,主要是通過瀝青浸漬法來降低氣孔率,即通過開口氣孔把煤瀝青浸漬到制品內部,然后通過二次焙燒,使瀝青焦化,填充孔隙。
浸漬的一般工序:先在具有良好密閉性的浸漬罐中對制品進行預熱,預熱溫度視所選浸漬瀝青的型號而定,通常在100℃左右;然后將浸漬罐抽真空,真空度控制在-0.06MPa左右,使制品脫氣;接著把熔化好的煤瀝青注入浸漬罐中,直至瀝青浸沒制品,同時給浸漬罐升溫,一般不超過300℃;最后給罐內加壓,促進瀝青進入制品內部,壓力一般不超過3MPa。
通常,等靜壓石墨要經過多次的浸漬—焙燒循環,但不超過3次,超過3次,浸漬工序對制品性能的提高作用就很有限了。清華大學在其公開專利《一種各向同性石墨制品及其制備方法》中,就采用了3次浸漬—焙燒循環工藝。浸漬后的樣品,在二次焙燒中,容易出現瀝青受熱滲出的現象,影響浸漬的效果。有研究表明,利用熱等靜壓技術對制品進行二次焙燒,在加熱的同時,施以5MPa左右的壓力,可以有效避免瀝青滲出現象。這種方法的缺點是,設備昂貴,生產率極低。
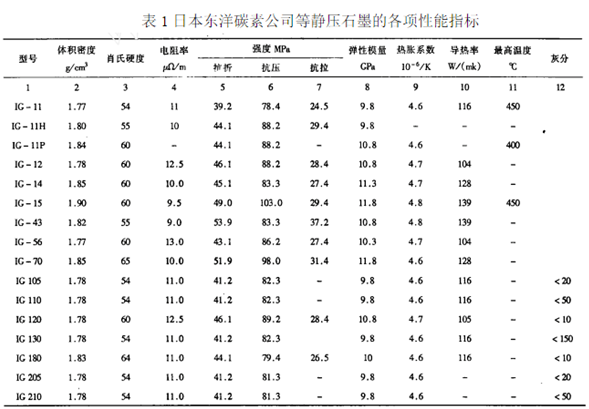
3.7 石墨化
把焙燒后的制品加熱到約3000℃,碳原子晶格有序排列,完成由炭向石墨的轉變的過程,叫石墨化。石墨化的方法有艾奇遜法、內熱串接法、高頻感應法等。通常的艾奇遜法,制品從裝爐到出爐,大約需1~1.5個月的時間。每爐可以處理幾噸到幾十噸的焙燒品。內熱串接法熱利用率高,約為艾奇遜法的1.5倍,已開始逐步取代艾奇遜法。石墨化后,制品的體積密度、導電率、導熱率及抗腐蝕性能得到很大程度的提高,機械加工性能也得到改善。但是,石墨化會降低制品的抗折強度。
3.8 檢驗
石墨化后,還需要對制品的密度、硬度、強度、電阻率、灰分等指標進行檢查,以判斷是否達到指標要求。表1為日本東洋碳素公司等靜壓石墨的各項性能指標。 表1日本東洋碳素公司等靜壓石墨的各項性能指標
3.9 純化
等靜壓石墨在用于半導體、單晶硅、原子能等領域時,對純度的要求很高,必須用化學方法將雜質除去后,才能用于這些領域。除去石墨中雜質的通常做法是,把石墨化制品放入鹵素氣體中加熱到約2000℃,雜質就被鹵化成低沸點的鹵化物而揮發除掉。幾乎所有的石墨化制品中的雜質元素均能用氯氣鹵化除掉。但是硼元素例外,它只能氟化除掉。用于提純的鹵素氣體有氯氣、氟氣,或者是能在高溫條件下分解產生這些氣體的鹵代烴,例如,四氯化碳( CCl4),二氯二氟甲烷( CCl2F2)。
例如美國的格拉弗技術國際控股有限公司在其公開專利《低CTE高各向同性石墨》中,就采用的高溫鹵素氣體除雜的方法:將石墨化得到的樣品在2200~2600℃之間經鹵素氣體純化,除去硼等雜質,得到高純度高各向同性石墨。
4.結語
在當今的工業生產中,石墨已經成為一種必不可少的關鍵材料,特別是在太陽能工業、半導體工業和核工業等方面,石墨的需求量在急劇增加,質量要求也越來越高。
目前,中國只能生產低品質的等靜壓石墨,高品質等靜壓石墨完全依賴進口。開發我國具有自主知識產權的高品質等靜壓石墨產品, 已經迫在眉睫,正待于我們迎頭趕上。
?歡迎進入【粉體論壇】
更多精彩!歡迎掃描下方二維碼關注中國粉體技術網官方微信(bjyyxtech)
|