電氣石是電氣石族礦物的總稱, 化學成分比較復雜, 其組成一般可表示為:(Na,Ca)(Mg,Fe,Li,Al)3Al6[Si6O18](BO3)3(OH)4,是以含硼為主的鋰、鈉、鐵、鎂、鋁的環狀結構硅酸鹽礦物?它基本上由以下三種端員組成: 鋰電氣石: Na (Li, Al)3Al6[Si6O18] (BO3) 3(OH) 4,黑電氣石: NaFe3Al6[ Si6O18](BO3) 3(OH) 4,鎂電氣石: NaMg3Al6[ Si6O18] ( BO3)3(OH)4,三者之間均可以成類質同象置換?
電氣石通常以黑色的常見,也有呈褐色、綠色、藍色、紅色、玫瑰色等,玻璃光澤,硬度7~ 7. 5,比重2. 9~ 3. 25。具有熱電性與壓電性?電氣石由于產地稀少,能形成開采規模的為數甚少,除作為寶石及磨料對待外,其工業應用至今仍是一個空白點。國內也很少有人從事電氣石工業加工、應用的研究探索?
最近,有一項專利技術是把電氣石應用于人造纖維絲中,即人造纖維絲中含有0. 5% ~ 2. 0%的電氣石粉體,其顆粒以不超過1~ 2m 為宜。該纖維具有優異的保暖性能,并可有效地促進人體的血液循環從而達到增強人體生理機能的目的,因此已被應用于保暖和保健內衣的生產中。根據某廠家的委托,我們對電氣石進行了超細研磨加工試驗,結果表明,采用干法超細粉碎,產品細度雖可滿足要求,但生產成本過高,不適合于工業化生產。而采用低速攪拌磨+高速攪拌磨的聯合磨礦工藝, 則產品完全可以達到工業利用的技術要求, 且在經濟上也是可行的?
1 試驗設備
1.1 試驗樣品
試驗用樣品為委托方提供的電氣石粉,呈深灰色,密度3.0 ~ 3.1g/ cm3,硬度7~7.5,中位粒徑(d50) 22. 95μm。其粒度分布見表1。
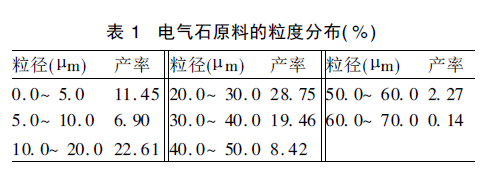
1.2 超細研磨及檢測設備
主要為濕式低速攪拌磨、濕式高速攪拌磨(帶冷卻夾套)和JL- 1155 型激光粒度分布測試儀。其它有隔膜泵、循環桶、制漿桶等。
2 電氣石超細研磨原理及工藝流程
根據我們的初步試驗表明, 單獨采用低速攪拌磨時,產品的細度不能達到規定的技術要求( 中位徑d50 0. 70μm, d95 2μm),在技術上不可行;而采用高速攪拌磨時產品細度可以滿足要求,但由于磨礦介質損耗很大, 成本過高, 在經濟上不可行。經過多次探索試驗,最后采用了低速攪拌磨循環磨礦+高速攪拌磨循環磨礦的聯合工藝,即將電氣石調漿后先在低速攪拌磨機上循環磨礦,直至粉體的細度達到d80 2μm,然后把漿料轉入高速攪拌磨機循環磨礦,直至產品細度合格。這樣即可保持較高的磨礦效率,又可把成本控制在合理的范圍內。
研磨過程是: 攪拌磨的攪拌棒攪動研磨礦介質,使介質作不規則運動而沖擊、剪切、摩擦,對物料進行粉碎。研磨前,先按比例將電氣石粉和水、分散劑在調漿桶中配成一定濃度的漿料, 然后泵送到裝有研磨礦介質的攪拌磨內,邊輸入漿料邊啟動攪拌軸。研磨后的漿料從溢流口流出至循環桶后,啟動攪拌器,調節隔膜泵的轉速,將桶內漿料通過磨機底部入口, 再輸回機內, 如此往復循環進行超細研磨,在研磨過程中每隔30min 取一次樣,進行粒度測定。直至粒度達到d80 2μm 后, 再按上述方法把漿料轉入高速攪拌磨中進行循環研磨,直至粒度合格,見圖1。
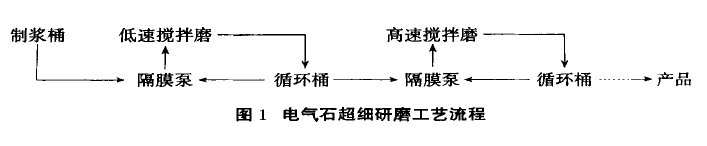
3 研磨試驗及結果及討論
3.1 研磨礦介質的選擇
研磨礦介質的密度及硬度對物料研磨效果起著重要作用, 一般情況下, 介質密度及硬度越大, 對物料的沖擊力也越大, 研磨效果也就越好。但由于電氣石是一種十分難磨的物料, 在長時間的研磨過程中, 磨礦介質損耗很大, 且大部分損耗是由于磨礦介質自身的碰撞而引起的, 特別是在高速攪拌磨中更加明顯。
在本研究過程中, 對氧化鋯和陶瓷磨礦介質進行了對比試驗, 試驗條件: 介質填充率67%,磨礦濃度67. 5%, 磨礦時間5h;試驗結果見表2。由表2 可見, 氧化鋯介質由于密度比氧化鋁介質大, 其研磨效率明顯好于氧化鋁介質, 損耗率也明顯低于氧化鋁介質, 但由于二者的價格相差6 倍以上(氧化鋯磨礦介質125 元/kg, 陶瓷磨礦介質20 元/kg ),因而采用氧化鋯磨礦介質的綜合成本反而大大高于氧化鋁磨礦介質。故在實際生產中, 選用了氧化鋁作為磨礦介質, 其配比如表3 所示。
3.2 漿料濃度試驗
不同物料,其研磨的漿料濃度也有所不同,實踐中曾將電氣石的漿料濃度控制在70 %,此時, 在初始階段物料的流動性良好, 但當電氣石的細度達到80% ~ 85%小于2μm時, 漿料的粘度迅速增加,物料的流動性變得極差, 磨機的研磨效率會明顯降低; 同時磨機進出口阻力急劇增加, 易造成篩網堵塞, 影響生產過程的穩定, 必須加入適量的分散劑方可使研磨繼續進行。為降低生產成本, 同時保持在較高的濃度下磨機具有較高的生產效率和穩定性,經多次試驗, 將電氣石的漿料濃度控制在65 % ,此時, 隨著研磨時間的延長, 漿料濃度雖有所增加,但不影響磨機的磨效和生產過程的穩定性。試驗條件: 陶瓷磨礦介質, 介質填充率67. 5%,研磨時間5h;結果見圖2。
3.3 介質填充率
在電氣石的超細研磨中, 介質填充率對物料的研磨效果也是一個重要的影響因素, 若介質填充過多, 則磨機內的物料相應減少, 反而引起研磨效率的下降, 同時由于介質自身碰撞等引起的損耗急劇增加; 若介質填充過少, 由于機內物料過多, 磨礦介質對電氣石的沖擊、剪切、摩擦相應減少, 同樣會引起研磨效率的下降。由圖3和圖4(試驗條件: 陶瓷磨礦介質, 礦漿濃度65%, 研磨時間5h)可見, 最佳的介質填充率為65% ~ 70% 。在此范圍內, 介質損耗適中, 研磨效率卻仍保持較高水平, 綜合經濟指標最高。同時, 在研磨過程中, 要始終保持介質填充率的相對穩定, 隨著介質的損耗, 需及時補加。根據本試驗的經驗, 在低速攪拌磨中, 可以每8h 添加一次, 而在高速攪拌磨中則需每4h 補加一次。
3.4 研磨時間的影響
電氣石中位粒徑(d50)變化與研磨時間的關系見圖5??梢婋S著研磨時間的延長, 電氣石粒徑逐漸減小, 但難度也隨之增大。在研磨初始階段, 由于其存在大量結構缺陷, 顆粒易粉碎, 但隨著研磨時間的延長和顆粒的細化, 顆粒結構缺陷減少, 粉碎能耗增大, 研磨難度隨之提高, 最后, 當研磨到一定細度時, 隨著研磨時間的延長, 電氣石的粒徑就會維持在一個平衡范圍內, 這即為理論上所謂的逆粉碎狀態。
根據上述試驗結果, 選定的磨礦時間為: 先低速攪拌磨研磨6h, 然后在高速攪拌磨中研磨4h, 其它試驗條件: 陶瓷磨礦介質, 介質填充率67.5%, 礦漿濃度65%。此時電氣石的細度可以達到中位徑d50 0. 70μm、d95 2μm的技術要求。
3.5 其它影響因素
分散劑一般用聚丙烯酸鹽類即可滿足要求, 其用量以保持研磨過程順暢為宜, 一般5~ 6kg/ t 干粉即可。采用高速攪拌磨生產時由于漿料溫度很高(可達70℃以上), 因此磨機和漿料循環桶必須加循環冷卻裝置。在研磨初始階段, 由于電氣石顆粒較粗, 易沉淀到磨機底部, 會卡死攪拌棒, 甚至燒毀電機, 一次停機時間不可超過10min。
4 產品技術和經濟指標
4.1 產品技術指標
超細電氣石產品中位徑d50 0. 67μm,其粒度分布見表5。
4.2 經濟指標
原礦經雷蒙磨機加工為325 目后的價格為2萬元/噸, 按本試驗確定的研磨工藝條件對1噸電氣石進行的中試表明, 其加工成本(含烘干成本)為3500 元/噸, 而超細電氣石粉的市場售價則可達4~5 萬元/噸, 因此具有較好的利潤空間。
5 結語
電氣石是一種難磨的工業礦物原料, 若選用干法超細粉碎, 則能耗過高, 生產成本過大; 其超細研磨宜選用濕法低速攪拌磨和高速攪拌磨相結合的工藝, 其最經濟合理的研磨工藝為: 采用陶瓷研磨介質, 礦漿濃度65%, 介質填充率65%~ 70% 。電氣石的最終細度達到d50 0.70μm, d95 2μm,可以作為人造纖維絲的功能性填料, 具有很好的經濟效益。
|